A quick online search for the term “tire recycling machines” will bring up hundreds of results from manufacturers of waste rubble pyrolysis plant equipment. With a pyrolysis reactor, it’s possible to convert scrap tires into useful materials via a completely pollution-free process. By heating waste rubber to high temperature in a sealed, oxygen-free chamber, rubber vaporizes instead of burning. The oil vapor can then be reliquified into fuel oils of different viscosities using a sophisticated water-cooled condensing system. The pyrolysis process really is ingenious and has allowed for the environmentally friendly disposal of scrap tires, as well as other types of waste materials including plastics and rubber. Get a tire recycling machine for sale to start your business.
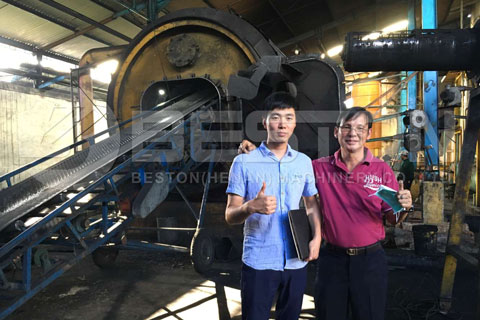
It is clear to see why pyrolysis tire recycling machines are now so popular around the globe. After all, waste tires can take hundreds of years to decompose in sea fill and landfill, and during the decomposing process, toxins are released into the natural environment. While many waste processing facilities have taken to incinerating mounting scrap tires and utilizing the heat, burning rubber results in dozens of pollutants being put into the atmosphere. Reputable pyrolysis machine manufacturers provide qualified machine with environmental-friendly system.
With a rubber pyrolysis machine, waste tire processing facilities can start to generate huge profits. Furthermore, they can earn eco-warrior green credentials from governments in many countries. Such credentials often allow a facility to access grants and subsidies for their contribution to environmentally friendly recycling.
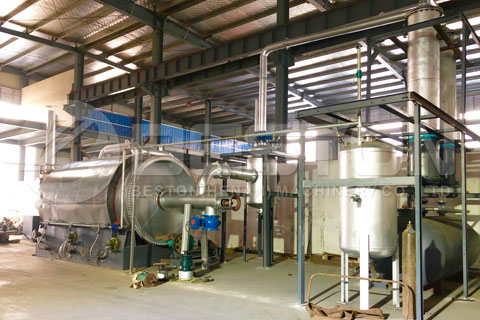
There are many different models of pyrolysis tire plants available in the global market space. Some of the basic specifications you need to find out when comparing models include reactor size, daily processing capacity, working method, operating pressure, heating materials, reactor pattern, floor area, life span, cost, cooling method and total power. Pyrolysis machine working method can be classified as batch, fully continuous or semi-continuous. A top-of-the-line fully continuous waste rubber recycling plant can process over 35 tons of raw materials daily.
When it comes to the end products generated from a waste tire pyrolysis recycling plant, all of them can be very profitable. A typically car tire contains 50% fuel oil, 30% carbon black and 15% steel wire. Combustible gasses are also produced during the pyrolysis process and they are generally recycled back through the plant to heat the reactor. Fuel oil and carbon black both have a wide range of applications, which gives them high commercial value. Many tire recycling facility operators invest in further equipment, such as a distillation machine, to convert tire oil into diesel oil and gasoline.